Position and orientation in space
Each physical component in the gearbox and the gear_unit itself has a local coordinate system. The position and orientation (POSE) of this coordinate system in space is described relative to the coordinate system of another component. Global specification of the POSE can be made when the gear_unit component is selected as the reference component. The user must ensure that the interface can determine the precise POSE of all components using these relative specifications. This will be explained in more detail in the requirements for precise positioning section.
Coordinate system specifications
A three-dimensional, right-hand, orthogonal, Cartesian coordinate system is used. The unit of measurement is millimeters (mm).
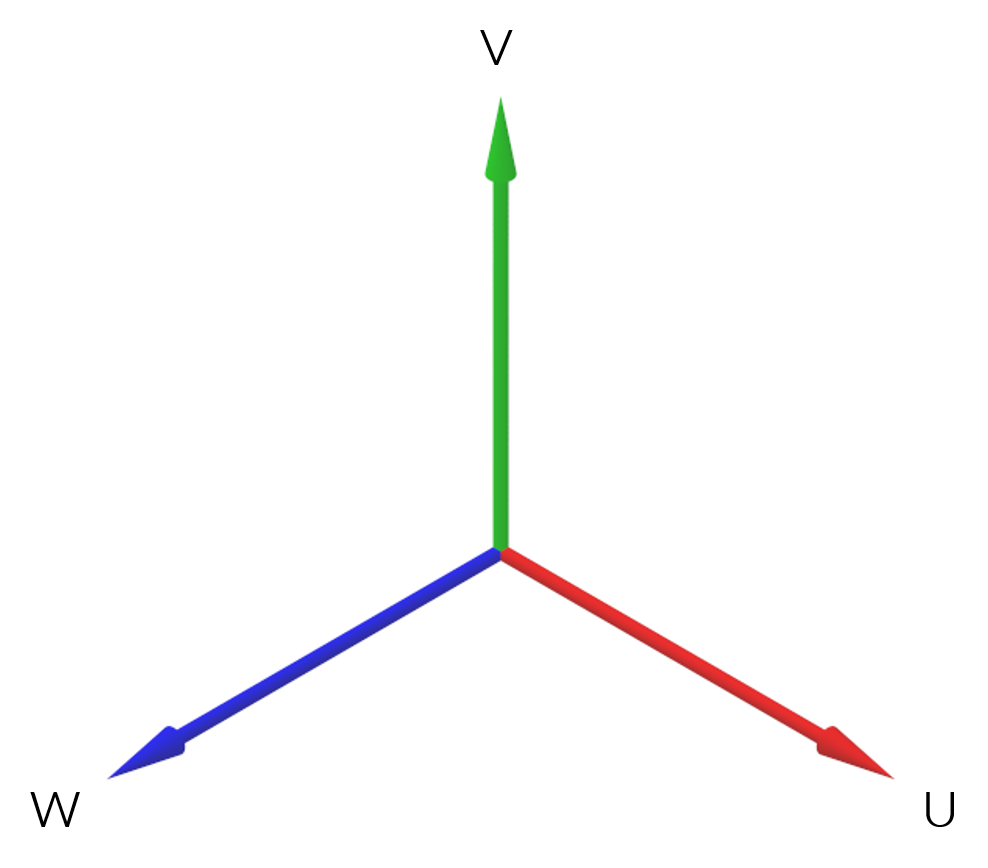
Each component has a local coordinate system with u, v, and w axes. A vector in the local coordinate system is described by three coordinates, indicated with u, v, and w.
Relevant attributes
Each component includes the following four attributes to describe the position and orientation (POSE) of the local coordinate system in space:
reference_component_for_position
support_vector
u_axis_vector
w_axis_vector
The reference_component_for_position attribute includes the ID of the component on which the coordinates of the POSE are based.
The support_vector specifies the position of the origin of the local coordinate system of the component relative to the coordinate system of the reference component.
This specifies the precise position of the component.
The u_axis_vector specifies the orientation of the u-axis relative to the reference coordinate system.
The w_axis_vector specifies the orientation of the w-axis relative to the reference coordinate system.
This specifies the precise orientation of the component. Both vectors have a length of 1 mm.
Each vector attribute contains an array with the following three floating point values u, v, and w in order; e.g., support_vector = {u, v, w}.
Position-relevant gear data
The description of the location of the components must be consistent with the relevant gear data; e.g., with the center distance of a cylindrical stage. For example, this means that the center distance calculated from the position data should correspond to the center distance attribute, within a calculation tolerance. The exact value from the attribute can then be used for the gear calculation.
Requirements for consistent positioning
The following requirements must be met to ensure a clear determination of the POSE of all gearbox components in space:
The gear_unit component must be the reference component for at least one component.
The gear_unit component should refer to itself as a reference component.
If the network of relationships of all components of a gear unit are represented as a graph, it should be consistent and free of loops (corresponding to a tree structure). Each component corresponds to a node, which is connected if and only if the POSE of one component refers to the other.
In other words: Following the chain of reference components from any component should ultimately lead back to the gear_unit component. In particular, no loops are allowed in the chain.